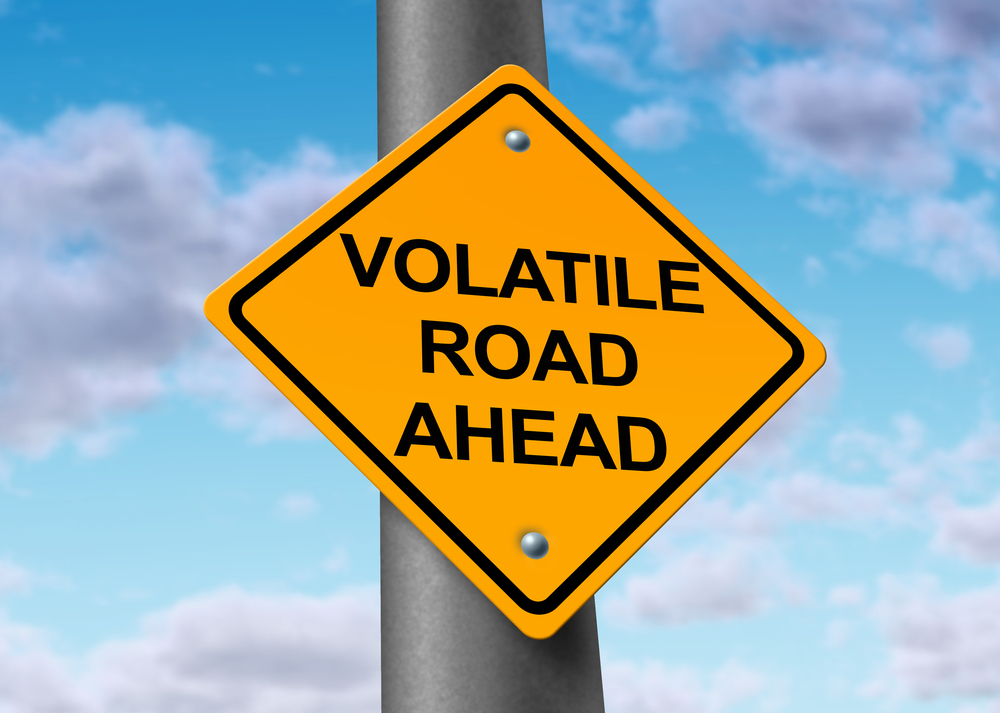
Information Technology plays a crucial role in the transformation of modern organizations. Technologies are revolutionizing effective, data-driven decision-making, increasing efficiency and reducing costs.
Whether for a project management office (PMO) or Lean portfolio (LPM), an IT service center (ITSM), your sales department or customer support, IT is a catalyst for productivity and innovation.
In the dynamic world (VUCA) where innovation and competition are fierce, continuous improvement is essential to stay at the cutting edge and accelerate the delivery of value.
This blog complements our previous articles on the Lean-Agile mindset, flow optimization, optimizing value flows
and focuses on the importance of continuous improvement for managers and directors wishing to maximize the efficiency and productivity of their IT departments.
Optimizing Today's Processes: An Evolving Necessity
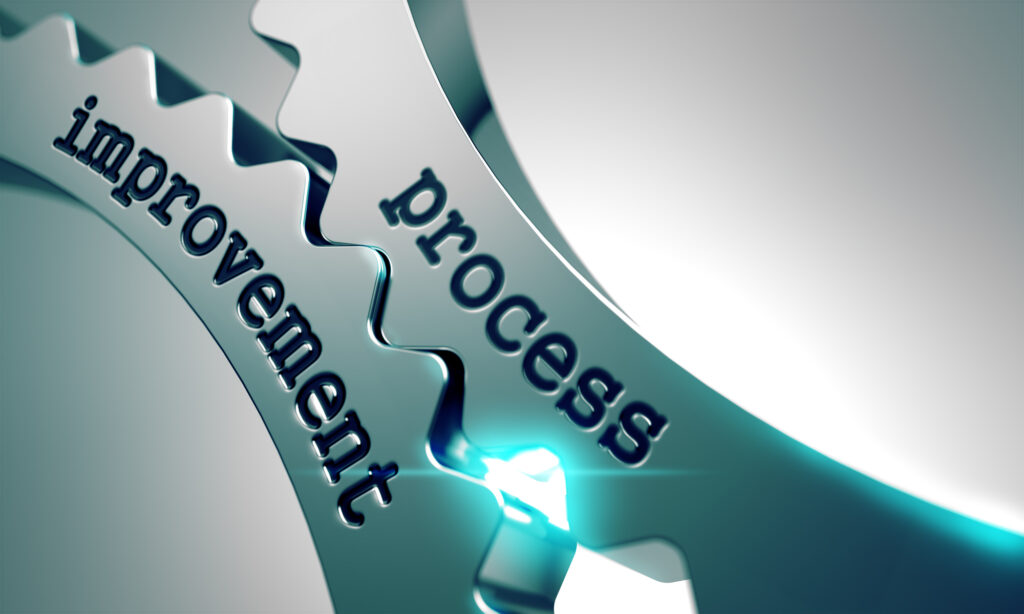
Continuous improvement in IT means more than just making one-off adjustments. It requires regular evaluation (PDCA) and review of current processes to ensure that they remain effective and relevant in the face of technological change and market demands.
Why Continuous Improvement?
Continuous improvement is a systematic methodology aimed at constantly improving processes, products or services by eliminating waste.
By regularly evaluating and revising your current processes, you can
🔍 Identify and eliminate inefficiencies
💸 Reduce costs
🌟 Improve product and service quality and customer satisfaction.
💡 Fostering innovation
Plan-Do-Check-Act (PDCA)
The Plan-Do-Check-Act (PDCA) cycle, also known as the Deming or Shewhart cycle, is an iterative management method used for the control and continuous improvement of processes and products. This model is widely applied in various fields, including information technology, to optimize processes and solve problems systematically.
Plan
In this phase, you identify a problem or an opportunity for improvement and define clear objectives. You analyze relevant data, evaluate current processes and propose potential solutions.
Do (to do)
During this phase, you implement the proposed solutions on a small scale to test their effectiveness.
Check
This stage consists of evaluating the results of the actions implemented. You compare the results obtained with the objectives set to determine the effectiveness of the solutions.
Act
Based on the results of the verification phase, you take steps to standardize improvements or adjust plans.
DMAIC
DMAIC is a data-driven improvement cycle used to optimize and stabilize business processes and designs. It is an integral part of the Six Sigma methodology. DMAIC stands for :
Define
Identify the problem, project objectives and customer requirements (internal and external).
Measure
Gather data and determine current process performance baseline.
Analyze
Examine data to identify the root causes of defects or problems.
Improve
Develop and implement solutions to address root causes and improve the process.
Check
Implement controls to sustain improvements, monitor the process and ensure that gains are maintained over time.
Each phase is crucial to ensuring that the problem is clearly understood, that improvements are effective, and that the process remains stable and consistent in achieving the desired results.
A3 management
A3 management is a structured approach to problem-solving and continuous improvement developed within the framework of Lean methodology, which originated with Toyota. The term "A3" refers to the size of the paper (A3: 11 x 17 inches) on which the process is usually documented.
This Lean management method emphasizes a systematic approach to problem solving, ensuring that the root cause of a problem is identified and addressed rather than simply treating the symptoms.
Seven PDCA-inspired steps to systematically structure and solve problems:
Step 1 Defining the problem, assessing sources of dissatisfaction.
Step 2: Assessment of current conditions.
Step 3: Goals & Targets
Step 4: Analysis of the current situation
Examples of tools used for analysis :
- Process mapping (VSM) Visualize workflows to identify weak points.
- Kanban management approach
- Performance analysis: Use key metrics to measure effectiveness.
- Ishikawa diagram, 5 Whys, decision tree, Pareto diagram, Six Sigma, etc.
Don't confuse analysis with countermeasures!
Step 5: Recommendations & Countermeasures
Step 6: The Plan
Step 7: Follow-up & Plan-Do-Check-Act in progress
Conclusion: Towards a Culture of Continuous Improvement
For company managers and directors, continuous improvement is more than a necessity - it's a strategic imperative. By integrating this approach into their day-to-day management, they can not only optimize and accelerate the delivery of value by their departments, but also ensure the sustainability and competitiveness of their organization. Continuous improvement must become an integral part of the corporate culture, where every team member is encouraged to contribute to process improvement and innovation.
In short, continuous improvement provides a robust framework for optimizing existing processes in a scalable way, ensuring that IT departments remain agile, efficient and focused on excellence.
About the author
With over 20 years of experience management Information Technology, Éric Auger helps companies accelerate their value delivery and optimize their organizational performance. IT consultant specializing in project management, Lean Six Sigma Green Belt Practitioner, Kanban management expert and Agility coachI combine strategy, tactics and operations to maximize your competitiveness in the digital age.
Passionate about digital transformationI work with organizations to optimize their value flowguaranteeing sustainable competitive advantage. I also like share my expertise and help professionals strengthen their skills in project management and agility.
Follow me for practical advice and proven strategies to make your projects a success.
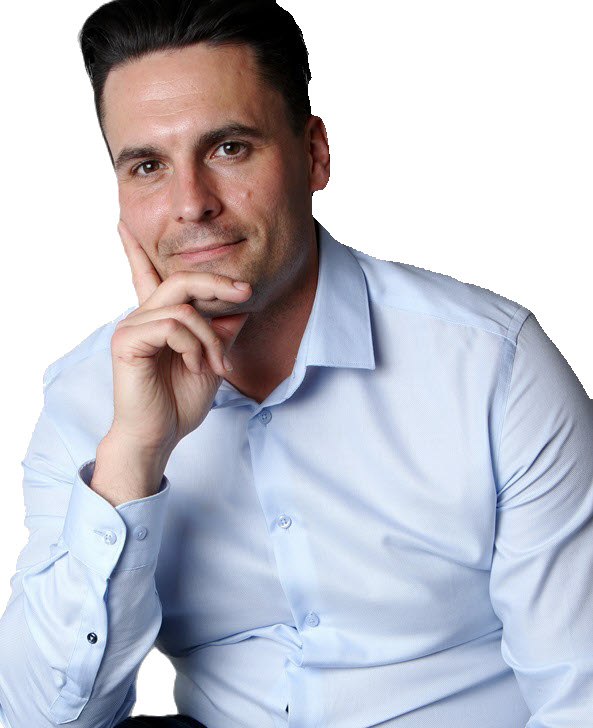